Rework is an industry-wide problem, reportedly representing up to 20% of total construction costs. We can only expect these numbers to surge, too, as the persistent industry trend pertaining to labor shortages remains prevalent. ForConstructionPros reported the industry’s dire need to add 546,000 additional workers on top of the normal pace of hiring in 2023 to meet the demand for labor.
As construction teams remain short-staffed, the probability for mistakes happening, and clients requesting rework to fix those mistakes, is likely to increase.
Scholarly studies show that, in addition to design errors, rework can occur as the result of many project management-level failures, such as:
- Poor project documents
- Conflicting/incomplete information
- Ineffective use of quality management practices/deviation due to poor monitoring
- Inadequate planning and poor scheduling of workload
- Inefficient management process, poor site management practice
And while preventing design-induced rework proactively through building information modeling is a well-cited approach, every part of the construction ecosystem has its own responsibility to bear in contributing to a project’s overall success as well as in delivering quality assurance of the work performed. In this article, I highlight the role inventory managers should play in ensuring onsite work runs smoothly without a hitch. I also offer four ways that efficient inventory management can help prevent rework.
The Role of the Inventory Manager in Construction Project Success
Construction inventory managers play a mission-critical role in safeguarding jobsite uptime relative to materials and equipment distribution.
Typical responsibilities for these professionals include:
- Overseeing the allocation, storage, and flow of all physical assets (e.g., building materials, tools, vehicles, and equipment) needed to perform construction work.
- Researching and implementing various construction logistical techniques and technologies to maintain unimpeded visibility to company assets across the entire supply chain such that equipment-related job uptime is maximized (e.g., cloud-based inventory management software, smart tools, tool and equipment tagging and IoT tracking products, etc.).
- Servicing inventoried assets to elongate their longevity and preventing jobsite-halting equipment breakdowns.
- Purchasing safety stock to prevent inopportune, job-stalling stockouts.
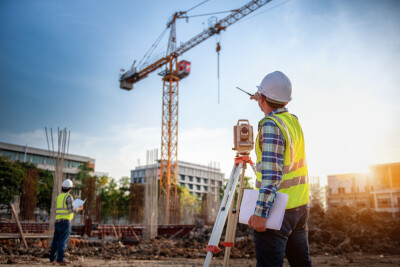
To contextualize the inventory manager’s role in preventing rework, consider the previously mentioned scholarly study. Poor quality of material ranked second in building projects and third in the overall ranking of 43 identified causes of rework in residential buildings. The list of rework causes under the “materials and equipment related factors” included, in addition to defective materials: Replacement or misplacement of materials and equipment, insufficient equipment use or altered materials, and untimely deliveries of materials and equipment. Putting this into context from a monetary measure: Industry research shows that 30% of all tool purchases are made because of loss or theft, and the industry loses between $300 million and $1 billion worth of large equipment like generators and construction vehicles every year.
However, it’s not so much the financial burden that errant assets or unexpected equipment breakdowns cause as much as how they impact jobs (e.g., lost productivity, quality problems, etc.).
With an effective inventory manager at the wheel of your logistics chain, equipment and materials-related rework and their associated costs can be minimized.
Four Ways to Prevent Rework through Efficient Inventory Management
Here are four examples of how efficient inventory management can contribute to rework mitigation:
1. Mastering Inventory Logistics
Inventory managers are logisticians at heart, the capable professionals you want at the helm of your construction supply chain.
By nature, an inventory manager knows how to deploy the appropriate resources where they’re needed, when they’re needed, as well as anticipating future need. Consider how supply chain wizard Tim Cook saved Apple from near bankruptcy in the late 90s, streamlining the company’s then-out-of-control supply chain, and contributing to its present-day success.
Construction supply chains are even more unpredictable, heightening the need of dynamic approaches like just-in-time-inventory. Such an approach has been seen to increase the efficacy of construction logistics by offering a distributed solution that can reduce the time and storage wasted from underutilized resources in component delivery.
Construction inventory managers offer a highly logistical skillset to optimize jobsite materials and equipment management:
Accurate Planners and Procurement Specialists
Inventory managers can properly gauge supply and demand across a complex, multi-jobsite ecosystem. They can help prevent hoarding, ensure proper procurement, and avoid shortages or excess materials. In doing so, they contribute to teams producing less materials waste and ensure jobsite progress, relative to equipment and materials, moves to schedule. Through maintaining project uptime, they can help prevent schedule overruns that would otherwise contribute to rushed work, increased safety hazards, and quality problems.
2. Implementing IoT Solutions
In addition to their planning and procurement skillsets, construction inventory managers are experts in adopting IoT technologies such as GPS, community Bluetooth® tracking, RFID, and NFC to help create digital breadcrumbs that connect the construction supply chain and deliver real-time visibility and inventory tracking.
Scholarly studies show that IoT solutions help inventory managers reduce waste, increase responsiveness, and perform real-time decision-making contributing to a more than 50% impact leading to positive opportunities.
- Barcodes/asset tags/RFID tags - Used in the warehouse to keep track of inventory shelf levels (and prevent stockouts).
- Bluetooth trackers and GPS trackers – Used to maintain real-time visibility to equipment as it’s sent from the tool crib across jobs and back.
- Near-field communication (NFC) – Capable to be used for rapid scanning and inventorying, as well as credentialing and security for personnel and preventing unauthorized access to sensitive areas where valuable inventory is stored and secured.
- Digital twin technology – IoT implementation plays an important role in helping inventory managers build digital twins to provide a more holistic view of the supply chain. Combined with advanced digital twin technology like artificial intelligence and machine learning, they can drive predictive decision-making for smarter forecasting, greater efficiency, and better performance outcomes.
Equipped with IoT technologies, inventory managers can help prevent materials and equipment-induced rework by:
- Performing real-time inventory auditing and reconciliation – With an interconnected supply chain, inventory managers are better equipped to reconcile physical quantities with recorded quantities and identify discrepancies early while reducing the likelihood that rework occurs due to missing, misplaced, or damaged materials; should materials be viewed as substandard, what’s more they can reroute replacements in real-time through their supplier network and ensure work gets completed on schedule with adequate materials and properly functioning tools and equipment (i.e., ensuring quality).
- Performing accurate forecasting and trends – Using historical data, trends, and artificial intelligence, inventory managers can predictively forecast with a greater degree of certainty, which can help improve planning and prevent both underestimation and overestimation of material/equipment needs, helping projects stay on budget and preventing rework due to materials or equipment shortage.
- Standardizing materials – By forming a firmer grasp on construction supply and demand across the company’s ongoing projects, inventory managers can better understand and, in turn, start to standardize the “tooling up” of jobs, reducing the risk of ordering incorrect materials and improving jobsite planning and scheduling of work and accompanying materials deliveries.
3. Smart Tools Delivering Better Project Outcomes at the Installation-Level
As with the industry-wide labor deficits, a skilled trade gap is widening, which runs the quality risk.
Certainly one potential (albeit costly) solution are robots (like SAM, the bricklaying robot) that can help automate procedural, repetitive, and often dangerous tasks that needlessly put onsite workers in harm’s way.
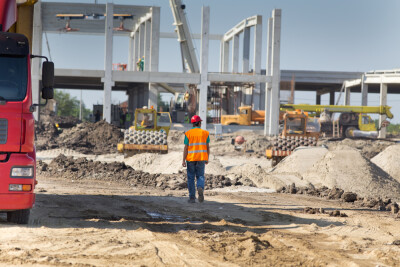
But even more accessible to companies looking to make a measurable impact at the inventory level, is tooling up jobs with smart tools, which provide a myriad of ways to improve quality at the installation level:
Quality reporting
Smart tools can provide peace of mind to customers that work will be completed to manufacturer specification and assure quality and efficacy of installation.
Onboard IoT sensors embedded in smart tools can pull utilization data in real-time as events are performed on the tool and synced to the cloud; this utilization data can then be fed into customizable dashboards that can be used for QA reporting.
Time savings
Customizable modes can help installers modify their tool’s performance for the job at hand, which in turn can help save time on the job by ensuring the tools are set up for the application ahead of the job; these modes can be synced to the cloud (virtually limitless customization) and applied on-tool depending on the day/task, as well as applied broadly across entire inventories.
Improved safety
In addition to installations being performed measurably faster and with greater accuracy through these precision settings, onboard machine learning helps prevent against dangerous kickback events, which can be hazardous both to the operator as well as running the risk of damaging materials (and further increasing the likelihood that rework will be needed). Thanks to these improved safety features, smart tools can help prevent rework and keep operators (both skilled trades and learning apprentices) safer.
Security and tracking come standard
In addition to all the above-mentioned benefits that the onboard IoT sensors provide smart tools, these tools can also be tracked wirelessly via an onboard Bluetooth® module – what’s more, through geofencing, these tools can be assigned to jobsites, and should they start to wander off-jobsite, owners will get notified. If they suspect unauthorized use, they can mark these tools “missing” or “stolen,” and, as these tools are seen by the Bluetooth network, they’ll lock out, rendering them useless to thieves, and only unlocked by the authorized owner.
In addition, this lock-out feature can be used to lock-out dangerous equipment (e.g., table saws, miter saws, etc.) left on active jobsite afterhours, which can help prevent unauthorized use and protect companies against potential liability were an accident could otherwise occur.
4. Being a Team Player through Data Sharing
I’ve previously written about the importance of construction technologists building toward interoperability; as well, I’ve discussed how BIM interoperability can help drive more positive outcomes by reducing data duplication, miscommunication that occurs through information silos, and so forth.
The same goes for inventory. Through data synchronization with integrations—like with BIM and project management platforms—inventory managers can help prevent duplicate project management information as well as share critical equipment-related updates (e.g., jobsite tracking alerts, reports from torque wrenches, etc.) with stakeholders like construction project managers so the team can work in lockstep in making decisions about worker utilization in order to keep projects moving along.
Final Word
Rework is a costly nightmare the entire industry is well-versed in, an expensive standard worthy of turning on its head. In that vein, every part of the construction ecosystem—from BIM modelers to architects to skilled trades onsite—need to work collaboratively to reduce the likelihood that rework is needed on a given job. Inventory managers, too, play a critical role. Through mastering the construction logistics chain, implementing IoT solutions, tooling up jobs with smart tools, and improving data synchronization enterprise-wide, inventory managers play their part in preventing rework for good.