“Well, early on, we didn’t want anyone to know,” said Simon Boyes, asked about his early days of implementing laser scanning into his workflows in the scaffolding business. Boyes was at least among the first to start using this technology specifically for scaffolding, if not the first. Typically we think of laser scanning in other contexts, like scanning buildings before, during, and/or after construction projects, or infrastructure like bridges and power lines for inspection purposes, but Boyes was growing increasingly frustrated with more traditional workflows and ultimately started to use a Trimble X7 for his scaffolding work, finding great success. He took a few minutes to speak with Geo Week News recently to talk about his story of getting started with 3D laser scanning, and the trends he’s seeing with these tools specifically in the world of scaffolding.
With over a decade of experience in scaffolding with roles viewing the industry from a few different perspectives, Boyes brings a unique perspective to this conversation regarding shifting workflows. Currently, he works as a managing director with Benchmark Scaffolding out of Australia, while also serving as an executive committee member with the Scaffolding Association Queensland. In addition to those roles, he’s also the founder of ScaffPlan, a software solution built on Trimble’s Tekla specifically for automating design and engineering processes in scaffolding. While that quote at the top of this page suggests he’s trying to keep his laser scanning close to the vest, that was only early on and he’s now at the forefront of trying to make it more common throughout the industry, recently writing an article for Scaffmag* discussing some of the value that’s been added to his work by utilizing this technology.
To get an idea of how his shift towards these scanning solutions ended up taking place, it helps to get a picture of what the workflow looked like before the change. Boyes told Geo Week News, “Normally, the customer will just send me a set of PDF drawings with some markups from the architect, but the problem is people come along and they change things, and they add things, and all that information doesn’t get updated in the drawing.”
As a result, Boyes and his team would have to do a lot of back and forth to and from a job site, taking photos and measurements. Back in the office, they’d sketch out the drawing for all of the scaffolding to fit around whatever was necessary for this project, but inevitably things would be forgotten or measurements would be off slightly, and more trips to and from the site were necessary.
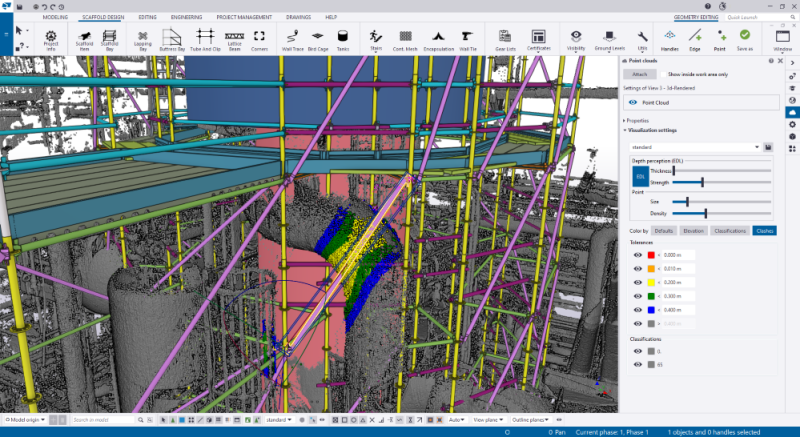
However, too often there would be a missing or incorrect measurement, or something else they forgot, meaning people had to go back to the site. Simply put, they needed a more efficient workflow. Initially, Boyes started with 360-degree photography to meet these needs. But then, Boyes said, “We realized we could take it another step further with scanning to really get millimeter precision measurements.”
It was interesting speaking with Boyes about these initial stages of his foray into laser scanning given his perspective as a relative outsider to the space. Obviously working in scaffolding there’s a fair amount of overlap with other AEC professionals, so there was a network on which he could lean for some information, but he describes something of a trial and error approach. One of the biggest challenges early on, Boyes said, was simply understanding all of the different scanning options on the market. He said at first they simply opted for the cheapest scanner they could find, and while that worked okay they eventually realized if they wanted to remain a leader in this space they’d need to look for a more high-end option.
Eventually, as noted above, they opted to switch to the Trimble X7. Boyes notes that they had already been using other Trimble offerings like Tekla Structures and SketchUp, so it made the most sense to stay in the Trimble ecosystem and simplify any integration processes. And in terms of actually using the scanner, he reported no issues. Asked about the learning curve in terms of actually operating the hardware, Boyes said, “That was a bit of a hesitation when we first started because we thought it was going to be too complicated. We don’t know what we’re doing here. But it’s as simple as set it up, press the button, and scan straight to a tablet.” He called concerns about complexity a “real misconception.”
Boyes and his team started using this technology “five or six years ago,” and the improvement to their workflow has been readily apparent. “It saves so much time because there’s no guesswork,” Boyes said, continuing, “Yes, it saves time. But the real value is when the guys turn up to actually install the scaffolding. It’s perfect. There’s no guesswork, there’s no rework. We know the exact quantity of materials that we need to take to the job, so there’s transport efficiencies. We know if we’re going to be short on materials before we start the job.”
After starting almost in isolation within the industry with this technology, Boyes has seen a real uptick in usage throughout the scaffolding space over the last few years, though “it still hasn’t been adopted as much as it should have.” A lot of the barriers he describes in getting broader adoption echo what we hear in the AEC industry more broadly, with firms having established processes that are already working. It’s hard to get people out of that rhythm, but he sees more uptick coming. “It’s a certain mindset, certain type of people that are willing to change. It’s more so the younger generation. I think as time goes on, it’s going to become the norm.”
He’s making that bet with his newest venture as well, with his creation of ScaffPlan, a software solution for scaffolding design and engineering. With Benchmark, Boyes and his team “built scaffolding design tools on top of Tekla Structures, and used that internally for probably three or four years.”
They realized how powerful the solution truly can be, particularly when you integrate things like laser scanning data and put everything into the Trimble ecosystem. “We realized it was a whole other business on its own.” Boyes believes it has the potential to be bigger than what Benchmark’s scaffolding business is, even.
Scaffolding has been around in some form all the way back to ancient times – scaffold-like structures were used in the construction of the Great Wall of China, as an example – meaning that workflows are well established and hard to change. Working past those stubborn ideals can pay dividends, though, as Boyes himself has shown with his experience in using laser scanning in his workflow.
“When the guys turn up on site, they know the drawings are going to be perfect," Boyes said of the benefits he's seen since making the switch. "They don’t have to think for themselves, they don’t come up against any unforeseen challenges they have to try and workshop themselves. It’s probably a four- or five-piece efficiency.”
*Boyes' article can be found on page 32 following that link.