Infrastructure is one of the topics on the minds of many in the United States and around the world. Accidents resulting from aging infrastructure have put the risks on the front of people’s minds, and particularly in the U.S., many structures such as bridges and dams are reaching an age where risk of some sort of failure is increasing with each passing year. This situation has led to legislation and awareness campaigns, in addition to renovation and replacement projects for all types of infrastructure.
While there is a lot of work to do to ensure durability of our infrastructure, we are also in an age where new technology can make inspections much safer for those on the ground and make the entire process much more efficient. Bentley Systems is among the companies in the middle of this innovation, helping these infrastructure owners create accurate models of these structures connected to all types of data points, including survey artifacts, 3D/2D designs, GIS, and various Internet of Things (IoT) sensors, to provide full context of their infrastructure.
Geo Week News recently spoke with Bentley’s Dustin Parkman, vice president, transportation, and Gregg Herrin, vice president, water. Parkman spoke to how this digital twin workflow has assisted in bridge inspections, while Herrin discussed the impact on dam inspections.
What is the workflow?
In terms of bridge and dam inspections, while the structures are quite different, the workflow for maintaining them with digital twins is similar, coming in three stages. The first is creating a reality mesh using laser scanning and/or photogrammetry, with Parkman noting that the best results come from a combination of the two. Much of this work is done by flying drones around a structure, as it is much easier to get all necessary angles with a drone than a terrestrial scanner. That said, they are also used for some pieces, and for bridges, even a mobile scanner on a boat can be used.
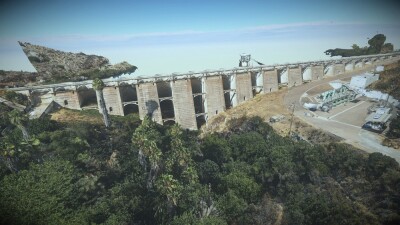
It creates an accurate 3D model of the structure, but to truly create a digital twin, it needs to be connected to sensors for real-time information. In bridges, according to Parkman, these sensors are capturing structural movement and scour, while also monitoring how much usage it is getting, how it is reacting to different climate events, as well as geotechnical sensors. Similarly, Herrin relays that dam inspection is assisted by piezometers monitoring groundwater pressure, as well as sensors monitoring for strength in joints, cracks on the surface of the dam, and vibration of the surface.
Of course, none of this matters without the software to make all of this data accessible to those monitoring and inspecting the structures, and that is where Bentley comes in. Bentley offers software to turn that reality capture data into a model, as well as software designed to aggregate IoT data into workable and accessible formats. It can all then be wrapped into a singular digital twin, giving an accurate 3D model with real-time information coming across from the IoT sensors. Herrin also notes that he is starting to see some companies, such as HDR, “extend these technologies with their own intellectual properties, using some of their own artificial intelligence capabilities to identify anomalies with the Murray Dam and Diablo Dam projects.”
Safer and more efficient workflows
Inspections have always been necessary for these kinds of critical structures. However, being able to do them as often and accurately as we would like has traditionally been easier said than done, particularly in safe ways. Both Parkman and Herrin noted the advantages seen by using this digital twin workflow.
It makes sense that having this data would improve these workflows, as much of the work can now be done remotely and virtually. Instead of manually inspecting an entire structure for cracks or other anomalies, inspectors can look for them within the model—sometimes using artificial intelligence to identify potential areas of concern—and send people to those specific locations. Similarly, sensors can pick up on potential issues well before they would become noticeable to humans, making repair significantly easier, cheaper, and safer.
For bridges, Parkman notes that teams have “saved over 30% on inspection hours and fees, with significant improvement in the quantity and quality of the deliverables.” More indirectly, too, he expects “to see a minimum of 20% construction savings stemming from the improvements in the quality of inspection data since better data leads to better decisions, thus reducing the risk of design errors or applying the wrong repair and rehabilitation solutions.”
Looking specifically at dams, Herrin reports many of the same benefits, though with some aspects unique to these structures. For example, much of the manual inspection of a dam involves inspectors using a rope to drop down the concrete wall of a dam or a slippery spillway downstream of gates, which can be very dangerous. By first inspecting the structure for issues using the reality model, you can identify problem areas and allow those inspectors to access only those spots, reducing the overall time they are spending in a dangerous location.
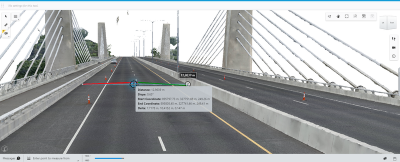
There are also financial savings here, which Herrin has seen firsthand. “One dam owner, who has multiple dams in its portfolio, was able to use our dam monitoring solution to save a huge amount of money on condition monitoring,” he told Geo Week News. “Their standard operating procedures used to cost roughly USD 3,000 per day, so by implementing digital technology, they were able to have a return on their investment in less than two months.”
Digital twins in action
While this kind of workflow of bringing reality capture and IoT data together for a real-time digital twin is relatively new for infrastructure monitoring and inspection, there are already plenty of examples. In fact, Parkman says that it got started out of these individual asset owners taking it on themselves.
He said, “It started off with our user base and customer base doing this on their own, piecemealing different pieces of our portfolio and our partners’ portfolio to do this. As we saw different elements coming together, we really saw an opportunity to pull a lot of these disparate pieces together into a well-integrated solution that allowed all these different data points to come into a digital twin.”
Bentley has noted a number of these projects for both bridges and dams. In Denver, for example, they must monitor 630 bridges throughout the county to ensure they remain safe for passage. Working with Stantec, they created digital twins for their bridges connected with IoT sensors, setting up customized alerts when movement of the structure exceeds pre-set parameters.
On the dam side, Perris Dam is an important structure in the state of California, and it was flagged for needing structural upgrades given risk during a seismic event. During the seismic retrofit project, Terracon (who was contracted for the project) and the California Department of Water used Bentley software with on-site sensors to monitor things like groundwater pore pressure and other structural issues throughout the project, providing easy web-access to both near real-time data and historic data.
Both Parkman and Herrin anticipate that legislation like the 2021 Infrastructure Investment and Jobs Act will impact this work, and money will continue to pour into the space as inspections will become more urgent and common. This workflow using reality capture and IoT sensors for real-time digital twins will make those inspections take less time and keep the workers on the ground safer.