The last half-decade or so has been a transformative one in the construction industry as it continues to embrace new technology and methodology at a rapid pace. After continuous realizations that the industry as a whole is much less efficient than it should be considering its size and impact on the entire world, the shifts have been quick and substantial. Just a few years ago much of the technology that is now commonplace on many job sites was little more than theoretical, and while there is still room to grow the industry and its workers are showing an appetite for adaptation.
Brasfield & Gorrie is one of the largest construction firms in the United States, based in the Southeast and handling major projects throughout the region and beyond for everything from entertainment venues, healthcare, education and more. Unsurprisingly given their place in the industry, they have also been more than willing to adapt new technology to ensure they are completing their projects as well and efficiently as possible.
Recently, Ryan Hittie and Kyle Duncan, both of whom work in Brasfield & Gorrie’s Innovation Department, took some time to speak with Geo Week News. In the conversation, the duo discussed how their implementing new technology – specifically drone imagery along with GIS-aided “digital dig boards” of job sites – into their projects, what that’s added to their work, and some other tools they’re working on for the future.
A look at the modern construction workflow
Hittie and Duncan work with the drone and GIS programs, respectively, and as they tell it their work certainly coincides and complements each other to provide crucial, accurate, and easy-to-use information to those in the field. Hittie describes the traditional workflow with drone mapping, which has evolved over the years from the firm having just one drone in 2017 to having 38 drones on different job sites by the end of this year. Traditionally, he says, they would fly the drone over the site and overlay the map of underground assets over the drone map.
That led to some new challenges, though, as they collected more and more data. He said, “That was great until we realized we’re getting more data, and every week this map looks different. This pile of lumber is here, but not on this dig board, so we’re going to have to print another dig board and that’s cost prohibitive and not logistically feasible to print a six-by-six dig board every week.”
That’s where Duncan’s work on the GIS side came in to help solve the issue, working with Esri tools. “We brought in Esri as a GIS platform to be able to remove the paper mill, if you will, from the project, using Site Scan as one example.”
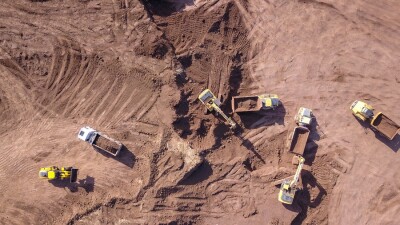
Using Site Scan, they were able to take the drone imagery and overlay that with CAD files collected from their contract documents or field engineers on-site, and have that oriented correctly to have that accurate depiction of the site. Duncan compared that to using satellite imagery, which may be significantly older and thus not as accurate, or even have issues like cloud covering which are not a problem with the drone imagery.
Making everything as simple as possible
When talking about implementing new technology into construction workflows, it’s one thing for the company to broadly talk about implementing these tools and the ways it can enhance projects. It’s an entirely different and more complex discussion, however, when talking about the actual implementation for those in the field. There is a reputation for the industry being stubborn in taking these steps, and while some of that is unfair there is at least some element of truth to that. B&G recognized this, and both Hittie and Duncan emphasized the need for simplicity in making this “digital dig board” technology work.
Specifically, they made sure that those in the field would be able to access and work with the information using technology and devices with which they already had familiarity. All around the job site are QR codes to pull up these digital dig boards. QR codes have in the past caused some confusion for those unfamiliar, but that is becoming a rare instance as QR codes are becoming commonplace outside of work since the start of the COVID-19 pandemic.
They also made sure to make the interface for the resulting ArcGIS Online portal as simple as possible with as few buttons as they needed. Duncan noted that they spent about a year developing these solutions, using some trial and error to ensure that everything was as easy to use as possible for those in the field. Using technology is great, but you only reap the benefits when those in the field are able and willing to take advantage.
Talking about this, Hittie said, “We have QR codes on business card-sized stickers that operators can stick on the window of their cab, and everyday they have an updated dig board. Or the superintendent can put it on their hard hat, or on their shovel even. You can put it anywhere on the job site, so really we don’t give people the option to say, I don’t understand, or, it’s too hard for me to understand. You have your phone, and you use it every day, and you just take it out and there’s the platform.”
Reaping the benefits
While it can be hard to pin down exact numbers to describe how beneficial a new technology program is for a large company, particularly one like this which has just been implemented on a wide basis this year, both Hittie and Duncan had examples of how projects have benefitted from these digital dig boards.
For example, Hittie discussed a project the firm was working on in San Antonio in which an electrical sub contractor on the project was measuring the distance from a pole to the site trailer for a temporary power line. To do so, he was walking the line to measure in steps how far it was. When the drone pilot saw this, he told the sub that they had flown a drone over the site the day before and could just measure the distance digitally. Hittie said he just “tapped twice on the screen and found it was 150 feet” for the line, adding that the sub was “blown away that the site was already mapped and they could do measurements instantaneously.”
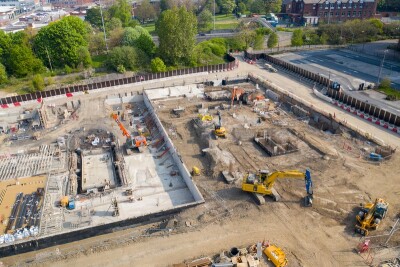
Duncan also talked about being able to work within the digital model to find these distances, noting an education facility they were building. He said there was already a crane pad on the site, and they were able to use the drone imagery in conjunction with their Esri tools to measure the area around the crane boom’s length and determine whether or not they’d be able to use the existing crane pad. As it turned out they did need to pour a new one, but he noted how quickly they were able to gather this information, whereas traditionally they likely would have just poured a new one from the start.
Continuing to look into the future
Working in the innovation department at B&G, Hittie and Duncan had been working on the above workflow prior to it being implemented into the field, and while they still are working with this they also discussed some other future-looking technology that can be implemented into construction workflows. For example, Hittie talked about autonomous construction equipment aided by drone mapping.
“On a greenfield site or turnover site, we can fly a lidar drone and get a very, very accurate topo map in just a couple of hours. From there, we have the new autonomous grading equipment, dozers and excavators, and we can send that surface file over to the equipment and say This is where you’re starting. It uses the GPS to locate itself, and the design team says, This is what it should be, and the equipment can automatically work until they meet the design surface.”
To be clear, this technology is not quite in use yet, and right now any work done with this equipment must be done with somebody in the cab pushing forwards in backwards, but the ability to use this is quickly approaching. Much like drones were more theoretical than practical on sites five to 10 years ago, autonomous grading equipment will quickly become a reality.
They also discussed emerging technology like augmented reality and advanced visualization, as well as utilizing more GNSS capabilities. Duncan said, “One thing we’re trying to do with digital twin access, specifically GPS data, we’re working a lot with GNSS and trying to add that into a living, working digital dig board, being able to not have the technical means of using a full total station but having a PM, superintendent, or even an intern able to take their phone and GNSS rover and go collect data and have it updated live to the board where everyone can see it.”